Warehouse Pallet Racking
Pallet racks are steel framed shelving used to store material on pallets. Pallet racks are sometimes called selective racks since, when properly positioned, each pallet can be selected individually by a forklift. It’s like having your stuff on a shelf. All your product can be accessed from the front face of the pallet rack. Since the back is open, you can also access it from the back, but generally pallet racks are set up back to back, or against a wall, since only one side needs to be accessible in order to get a pallet of product. Most warehouses are set up with racking back to back.
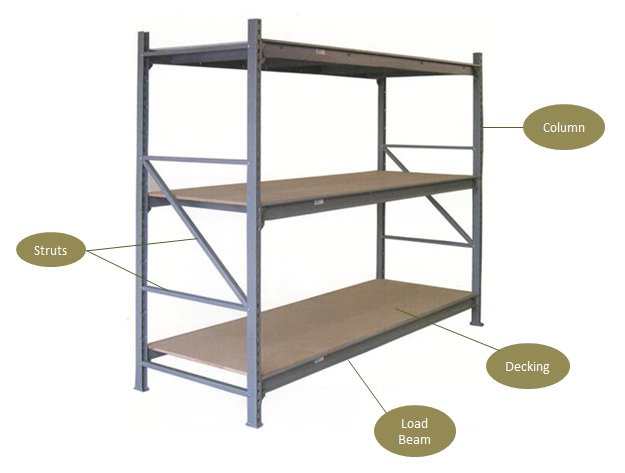
Warehouse pallet racking have certain standard components. The basic frame consists of the columns and struts that are welded together to form an upright, and the load beams. These are the three basic components of a pallet rack. Actually since the upright is considered one piece once it is fabricated, there are only two basic components. If you were to order pallet racks, you would receive uprights and load beams.
Each pallet rests on two load beams, the front and the back. This is why they are called load beams since they bear the load of the pallet. The decking is optional. Decking can be used to hold skids that are smaller than a standard pallet. They are also used as a safety measure in case a pallet isn’t aligned on the load beams. The decking will take the weight of a misaligned pallet. There are several options for decking including, wire mesh, wood planks, and steel plate.
Although pallet racks can be fabricated to any dimension, there are standard configurations. The most common size of pallet is 40” x 48”. Most pallet rack manufacturers recommend a three inch overhang at the front and the back of the rack. This brings the pallet rack depth to 42”. This is one standard depth for the upright. Other standards include 28”, 36”, 42”, 48” and 54”. The depth depends on the size of pallet you are planning to store on the rack. For some of the highest quality pallet racking systems, check out Schaefer Shelving.
The spacing of your uprights depends on how you want to configure the rack. In most cases, the weight of the load is the most important factor, however, it is standard practice to have an upright located every two pallets. So if your pallet rack is designed to store 4 pallets side by side, you would need 3 uprights, one for each side and one for the middle (between the second and third pallet). If your pallets are extremely heavy, uprights are placed between each pallet position.
The vertical spacing of the load beams depend on the height of your pallets. For most standard heights (40 to 60”) there is nothing to worry about, but if your skids are taller than five feet you may need additional support on your uprights, since everything is connected in one load bearing system.
The steel used to make pallet racks is either roll-formed or structural steel. The main difference between the two types of steel is load bearing capacity. Roll-formed steel is the standard material used to make most pallets racks, but for heavier loads structural steel is used.
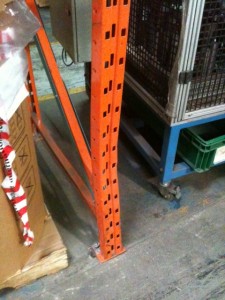
The process used to make roll formed steel for pallet racks is called cold roll forming. The sheets of cold steel are bent with rollers to form the shapes for the struts and uprights. For structural steel, the process is essentially the same, except the steel is shaped while hot. That’s right, structural steel frames are also roll formed, only they are hot roll formed.
However, the main difference is the type of steel used. Structural steel pallet racks are made of hot rolled channels of steel, while roll formed pallet racks are made with flat carbon steel. Roll formed racks are lighter and still have some flex in the steel. Structural steel racks are solid racks, with no flex designed to hold much greater loads.
Regardless of the fabrication process, what is important is the load bearing capabilities. Structural steel racks are designed to bear more weight. They are firmly fastened together with steel fasteners like nuts and bolts. Structural steel racks can handle a bit more abuse than a roll formed rack, but once they are bent there is no spring back in the steel. They will be permanently deformed and should be replaced.
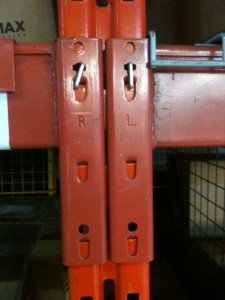
Load beams on roll formed racks have small metal tabs that clip into holes on the uprights. This makes them easier to install and adjust to the optimal height. This flexibility is an advantage, since they can be easily reconfigured if your needs changed. Another advantage of roll formed racks is that they are less expensive. And this is why they are the standard choice for most warehouse racking applications.
Be sure to check the weight of the pallets you are planning to store, to determine whether a structural steel rack is required or if you can survive with standard roll formed warehouse pallet racking.
Return to Main Warehouse Racking page.